CAMBIA LA TUA ORGANIZZAZIONE CON IL LEAN THINKING DI JAMES WOMACK
Come possiamo utilizzare i principi della lean manufacturing per migliorare le nostre aziende?
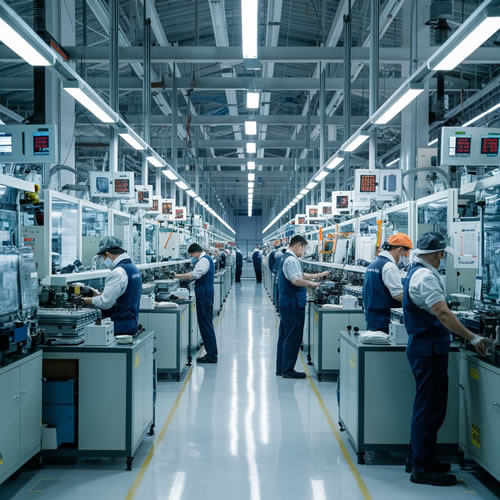
"Il Lean Thinking è una mentalità che trasforma ogni problema in un'opportunità per il miglioramento continuo"
(James P. Womack)
"Non migliorare mai ciò che si può eliminare"
(Henry Mintzberg)
Il lean lhinking o pensiero snello non è solo una metodologia, è una mentalità rivoluzionaria capace di trasformare il modo in cui le aziende operano, migliorando l'efficienza e riducendo gli sprechi. Co-sviluppato da James Womack, questo approccio si concentra sulla creazione di valore per il cliente attraverso l'ottimizzazione dei processi aziendali. Ma cosa significa davvero tutto questo? Ecco i cinque principi fondamentali della metodologia:
- Identificazione del valore: comprendere cosa il cliente finale considera come valore è fondamentale. Questo principio ci invita a focalizzarci sulle esigenze del cliente, eliminando tutto ciò che non contribuisce direttamente a soddisfarle. Le attività che non aggiungono valore sono sprechi e devono essere eliminate. Bisogna procedere comprendendo a fondo le esigenze e le aspettative del cliente e concentrarsi su attività e processi che contribuiscono a soddisfare queste esigenze
- Mappatura del flusso di valore: analizzare tutte le fasi del processo di produzione per identificare ed eliminare gli sprechi. Creare una mappa dettagliata che visualizza ogni passo necessario per creare il prodotto o servizio passando dal concetto al cliente finale. Una mappa dettagliata del flusso di valore serve a identificare i punti di miglioramento.e a distinguere chiaramente tra attività a valore aggiunto e quelle che ne sono prive
- Creazione di un flusso continuo: assicurarsi che il processo produttivo fluisca senza interruzioni. Ridurre i tempi di attesa, i colli di bottiglia e le inefficienze per mantenere la produzione costante e veloce aiuta a consegnare il valore al cliente in modo più rapido e fluido. occorre e liminare gli ostacoli che interrompono il flusso dei processi e ridurre i tempi di attesa e ottimizzare il movimento dei materiali e delle informazioni
- Implementazione di un sistema pull: produrre solo ciò che è richiesto dal cliente, evitando accumuli di scorte inutili. Un sistema pull è guidato dalla domanda effettiva, non dalle previsioni. Il principio del sistema pull si basa sull'idea che nulla deve essere prodotto fino a quando non c'è una domanda da parte del cliente. A differenza dei sistemi push, dove la produzione è basata su previsioni di domanda, un sistema pull produce solo ciò che è richiesto, riducendo l'inventario e gli sprechi associati alla sovrapproduzione
- Ricerca della perfezione: promuovere una cultura del miglioramento continuo. Tutti i membri dell'organizzazione devono cercare costantemente modi per ottimizzare i processi e aumentare il valore per il cliente. L'ultimo principio del Lean Thinking è la ricerca costante della perfezione. Anche quando i processi sembrano ottimizzati, c'è sempre spazio per miglioramenti. La perfezione è raggiunta attraverso un ciclo continuo di miglioramento (kaizen), coinvolgendo tutti i livelli dell'organizzazione nella ricerca di modi per migliorare e innovare. Bisogna promuovere una cultura del miglioramento continuo e incoraggiare tutti i dipendenti a contribuire con idee per migliorare i processi e ridurre gli sprechi
L'influenza di James Womack
James P. Womack è un nome di spicco nel mondo della gestione aziendale e della produzione snella. Economista e autore rispettato, Womack è noto soprattutto per il suo lavoro pionieristico nel campo del lean thinking, un approccio che ha rivoluzionato il modo in cui le aziende operano e competono a livello globale.
👤 Chi è James Womack? Ha conseguito il dottorato in scienze politiche presso il MIT, sviluppando un forte interesse per l'efficienza produttiva e i metodi di gestione aziendale. La sua carriera è decollata grazie al suo lavoro come ricercatore e docente, concentrandosi sull'industria automobilistica e sui metodi di produzione giapponesi, già allora all'avanguardia.
🌟 Il contributo di Womack al lean thinking Il contributo più significativo di James Womack è stato il co-sviluppo e la diffusione del pensiero snello. Questo approccio gestionale mira a massimizzare il valore per il cliente riducendo al minimo gli sprechi. Grazie a Womack, questi principi sono diventati accessibili e applicabili a una vasta gamma di settori, non solo all'industria automobilistica.
Uno dei momenti chiave della sua carriera è stata la pubblicazione del libro "The Machine That Changed the World", scritto insieme a Daniel Jones e a Daniel Roos. Questo libro ha messo in luce il successo del sistema di produzione Toyota (TPS) e ha introdotto il termine "lean production", mostrando come i principi del TPS potessero essere adattati e adottati da aziende di tutto il mondo per migliorare l'efficienza operativa.
James Womack ha giocato un ruolo cruciale nel diffondere una filosofia che ha trasformato il modo di fare business in tutto il mondo. Il suo contributo al lean thinking ha permesso alle aziende di qualsiasi settore di raggiungere livelli di efficienza e competitività senza precedenti, rendendolo una figura fondamentale nella gestione aziendale moderna.
Adottare il pensiero snello permette alle aziende di:
- rispondere più rapidamente alle esigenze dei clienti
- ridurre i costi operativi
- migliorare la qualità dei prodotti e dei servizi
L'importanza del lean thinking nell'industria moderna
Il lean thinking, nel tempo, si è affermato come uno degli approcci più efficaci per affrontare le sfide delle organizzazioni e la sua importanza nell'industria moderna è innegabile. Mira a a eliminare gli sprechi, o "muda" in giapponese, ossia tutte le attività che non aggiungono valore dal punto di vista del cliente. Riducendo o eliminando questi sprechi, le aziende possono abbattere i costi operativi e migliorare l'efficienza. I principali tipi di sprechi includono:
- sovrapproduzione: la sovrapproduzione si verifica quando si producono più prodotti di quanto richiesto dai clienti o prima che siano necessari. Questo tipo di spreco comporta l'accumulo di scorte inutili, che a loro volta generano ulteriori costi di stoccaggio e gestione. Esempi di sovrapproduzione sono la produzione di massa (fabbricare grandi lotti di prodotti senza ordini concreti, basandosi su previsioni di vendita non sempre accurate) e la stampa di materiale promozionale in eccesso (stampare volantini, brochure o cataloghi in quantità superiori alla domanda effettiva)
- attese: i tempi di attesa rappresentano i periodi in cui i materiali, le informazioni o i dipendenti rimangono inattivi in attesa che si completino altre attività. Questo spreco rallenta il flusso di lavoro e riduce l'efficienza complessiva. Esempi di attese sono i macchinari inutilizzati (macchinari che rimangono inattivi mentre si attendono i materiali o le approvazioni per iniziare una nuova produzione) e i ritardi nei feedback (tempi di attesa per le approvazioni dei supervisori o per i feedback sui progetti)
- trasporti: il trasporto include il movimento non necessario di materiali e prodotti all'interno o all'esterno dell'azienda. Ogni spostamento comporta costi aggiuntivi e aumenta il rischio di danneggiamenti. Esempi di trasporti sono la movimentazione interna (spostare materiali da un magazzino all'altro senza una reale necessità operativa) e la distribuzione inefficiente (trasportare prodotti finiti a magazzini distanti prima della spedizione al cliente finale)
- processi inutili: le fasi inutili dei processi sono attività o passaggi che non aggiungono valore al prodotto finale e che possono essere semplificati o eliminati. Questi passaggi aggiungono complessità e consumano risorse senza benefici concreti. Esempi sono la duplicazione delle attività (ridondanza di documenti o controlli che non sono necessari per garantire la qualità) e i compiti manuali ripetitivi (attività manuali che potrebbero essere automatizzate per aumentare l'efficienza)
- scorte: le scorte rappresentano i materiali, i semilavorati e i prodotti finiti che non vengono immediatamente utilizzati o venduti. Le scorte eccessive comportano costi di stoccaggio, deterioramento e obsolescenza. Esempi di scorte sono le materie prime in eccesso (acquistare e accumulare materie prime in grandi quantità senza una previsione accurata della domanda), un eccesso di prodotti finiti (tenere un livello alto di prodotti finiti a magazzino in attesa di ordini
- movimenti inutili: si riferiscono ai movimenti non necessari degli operatori durante il loro lavoro. Questi movimenti aumentano il tempo di completamento delle attività e possono causare affaticamento. Esempi di movimenti inutili: operatori che devono spostarsi per recuperare attrezzi o materiali e movimenti ripetitivi e non ergonomici che potrebbero essere evitati con una migliore organizzazione del posto di lavoro
- difetti: includono tutti i prodotti o i servizi che non soddisfano gli standard di qualità e richiedono rilavorazioni o scarti. Questo tipo di spreco comporta costi aggiuntivi per le correzioni e può danneggiare la reputazione dell'azienda. Esempi tipici sono i prodotti che non rispettano le specifiche tecniche e devono essere rilavorati o scartati e i servizi forniti con errori che richiedono ulteriori interventi per essere corretti
La lean manufacturing promuove una cultura di miglioramento continuo (kaizen), dove tutti i membri dell'organizzazione cercano costantemente modi per ottimizzare i processi. Questo porta a un perfezionamento delle attività e a un maggiore coinvolgimento dei dipendenti, che si sentono parte integrante del processo di miglioramento. Il miglioramento continuo consente alle aziende di essere più agili e reattive ai cambiamenti del mercato, mantenendo un vantaggio competitivo.
Applicando i principi del lean thinking, le aziende possono migliorare significativamente la qualità dei prodotti e servizi. Strumenti come il controllo statistico di processo (SPC), il metodo delle 5S e il Just-In-Time (JIT) aiutano a identificare e correggere i problemi di qualità alla fonte, riducendo i difetti e aumentando la soddisfazione del cliente. Una qualità superiore si traduce in maggiore fidelizzazione dei clienti, meno resi e riparazioni e una reputazione più solida sul mercato.
La capacità di adattarsi rapidamente ai cambiamenti è importantissima e il lean thinking, con il suo focus sul flusso continuo e sulla riduzione dei tempi di ciclo, permette alle aziende di essere più flessibili e reattive. L'implementazione di un sistema pull consente di produrre solo ciò che è effettivamente richiesto dal mercato, riducendo le scorte in eccesso e migliorando la capacità di rispondere alle variazioni della domanda. Adottare questa metodologia può fornire alle aziende un vantaggio competitivo significativo. Riducendo i costi, migliorando la qualità e aumentando la velocità di risposta, le aziende possono offrire prodotti migliori a prezzi più competitivi. Inoltre, una cultura del miglioramento continuo e del coinvolgimento dei dipendenti contribuisce a creare un ambiente di lavoro positivo e innovativo che attira e trattiene i migliori talenti.
Il concetto di valore nel lean thinking: La chiave del successo
Il valore è il pilastro centrale del lean thinking, rappresentando il punto di partenza per qualsiasi iniziativa di miglioramento dei processi. Definire correttamente il valore è cruciale, poiché tutto ciò che non contribuisce direttamente alla creazione di valore per il cliente finale è considerato uno spreco.
Cos'è il valore? Il valore è definito dal cliente e riguarda tutto ciò che il cliente è disposto a pagare. È determinato dalle sue esigenze, aspettative e desideri. Nel contesto dela lean manufacturing, il valore si riferisce alle caratteristiche del prodotto o del servizio che soddisfano le esigenze del cliente e giustificano il prezzo pagato. L'obiettivo è creare e offrire il massimo valore possibile al cliente, eliminando al contempo qualsiasi attività che non aggiunge valore.
Esempi di valore:
- qualità del prodotto: il cliente si aspetta che il prodotto funzioni correttamente e duri nel tempo
- tempistiche: il cliente desidera ricevere il prodotto o il servizio nel minor tempo possibile
- personalizzazione: il prodotto o il servizio deve soddisfare le specifiche esigenze del cliente.
Per identificare correttamente il valore, le organizzazioni devono partire da un'analisi approfondita delle esigenze e delle aspettative dei loro clienti attraverso sondaggi, interviste, analisi dei feedback e studio delle tendenze di mercato. L'obiettivo è ottenere una comprensione chiara di cosa è veramente importante per il cliente. Una volta identificato il valore, il passo successivo è eliminare tutte le attività che non contribuiscono direttamente alla creazione di questo valore. Queste attività sono considerate sprechi.
Creazione di valore continuo il lean thinking promuove la creazione continua di valore attraverso un ciclo di miglioramento continuo noto come kaizen. Questo implica che tutte le attività e i processi aziendali devono essere costantemente rivisti e ottimizzati per garantire che continuino a creare valore per il cliente nel modo più efficiente possibile. Per creare valore su base continua occorre:
- incoraggiare tutti i membri dell'organizzazione a identificare e suggerire miglioramenti
- fornire formazione continua per migliorare le competenze e la consapevolezza del personale riguardo ai principi del lean thinking
- applicare strumenti come il Value Stream Mapping, le 5S e il Just-In-Time per ottimizzare i processi.
Il flusso di valore comprende tutte le attività che trasformano una materia prima in un prodotto finito o in un servizio e questo include ogni fase del processo, dall'acquisizione delle materie prime alla produzione, alla logistica e alla consegna al cliente finale. Ogni passaggio nel flusso di valore dovrebbe essere esaminato per determinare se aggiunge valore dal punto di vista del cliente.
I componenti del flusso del valore sono :
- il flusso di materiali: movimento fisico dei materiali attraverso il processo produttivo
- il flusso di informazioni: dati e comunicazioni necessari per guidare il flusso di materiali e per prendere decisioni
- il flusso di lavoro: azioni e processi eseguiti dal personale per trasformare i materiali in prodotti finiti
I passaggi per la mappatura del flusso del valore sono:
- selezione del processo: identificare il processo specifico da analizzare
- raccolta dei dati: raccogliere informazioni dettagliate su ogni fase del processo, inclusi tempi di ciclo, tempi di attesa e movimentazione dei materiali
- creazione della mappa attuale: disegnare la mappa del flusso di valore attuale, evidenziando tutte le attività a valore aggiunto e prive di valore aggiunto
- analisi della mappa: identificare gli sprechi, i colli di bottiglia e le inefficienze nel processo
- progettazione della mappa futura: creare una mappa del flusso di valore ideale, che elimina gli sprechi e ottimizza le attività a valore aggiunto
Il passo successivo dopo l'eliminazione degli sprechi è creare un flusso continuo, in cui i materiali e le informazioni si muovono senza interruzioni attraverso il processo produttivo. Un flusso continuo riduce i tempi di ciclo e aumenta la velocità di risposta alle esigenze del cliente.Per creare un flusso continuo occorre:
- ridurre i tempi di attesa: minimizzare i tempi di attesa tra le fasi del processo
- bilanciamento del carico di lavoro: distribuire equamente il lavoro tra le diverse fasi del processo
- standardizzazione dei processi: stabilire metodi di lavoro standardizzati per garantire coerenza e qualità
- implementazione del pull system: produrre solo ciò che è richiesto dal cliente, basato sulla domanda reale
Kanban: una gestione visuale del lavoro
Il kanban è il metodo che ha rivoluzionato il flusso di lavoro e migliorato l'efficienza dei processi produttivi in tutto il mondo. Il termine "kanban" significa "cartellino" in giapponese. Nel contesto della gestione del lavoro, questa metodologia utilizza dei segnali visivi per indicare quando rifornire i materiali o passare alla fase successiva del processo produttivo.
Componenti del sistema kanban:
- cartellini: segnali visivi che indicano quando avviare, fermare o trasferire una fase del processo
- lavagna: mostra tutte le attività in corso, organizzate in colonne che rappresentano le diverse fasi del processo
- limiti WIP: limiti massimi al numero di attività in corso in una determinata fase, per evitare sovraccarichi.
Come funziona il kanban:
Definizione del flusso di lavoro:
- identificare le diverse fasi del processo, come "To Do" (Da fare), "In Progress" (In corso) e "Done" (Completato)
- creare una lavagna Kanban con colonne che rappresentano ciascuna fase
Creazione dei cartellini kanban:
- preparare cartellini che rappresentano le attività da svolgere, includendo descrizione, responsabile e data di scadenza
Limitazione del lavoro in corso (WIP):
- impostare limiti massimi al numero di attività in corso in ogni fase, per evitare sovraccarichi e migliorare il flusso di lavoro
Gestione visuale del lavoro:
- spostare i cartellini attraverso le colonne della lavagna kanban man mano che le attività avanzano
Feedback e miglioramento continuo:
- monitorare costantemente il flusso di lavoro e raccogliere feedback dai dipendenti. Utilizzare il ciclo PDCA (Plan-Do-Check-Act) per implementare cambiamenti.
Benefici del kanban:
- mMiglioramento della visibilità delle attività in corso: la gestione visiva del lavoro facilita il monitoraggio delle attività e l'identificazione di colli di bottiglia
- aumento dell'efficienza: limitare il lavoro in corso riduce i tempi di attesa e migliora il flusso
- riduzione degli sprechi: il kanban aiuta a identificare ed eliminare le attività non a valore aggiunto
- flessibilità e adattabilità: facilmente adattabile ai cambiamenti delle esigenze del mercato e dei clienti
- coinvolgimento del personale: la trasparenza del sistema kanban coinvolge attivamente i dipendenti, migliorando la comunicazione e la collaborazione
LA COLLANA DEI LIBRI DI QUALITIAMO -
"La nuova ISO 9001:2015 per riorganizzare, finalmente, l'azienda per processi" - Si aggiunge alla collana dei libri di QualitiAmo il primo testo che svela i segreti della futura norma.
Dalla teoria alla pratica: il secondo lavoro di Stefania Cordiani e Paolo Ruffatti spiega come migliorare la vostra organizzazione applicando la nuova norma attraverso i suggerimenti del loro primo libro
(Vai all'articolo che descrive il nuovo libro)"Organizzazione per processi e pensiero snello - Le PMI alla conquista del mercato" - Da una collaborazione nata sulle nostre pagine, un libro per far uscire le PMI dalla crisi.
L’ideatrice di QualitiAmo e una delle sue firme storiche spiegano come usare con efficacia la Qualità.
(Vai all'articolo che descrive il primo libro)
(Vuoi restare aggiornato gratuitamente sulla ISO 9001:2015? Visita ogni giorno la pagina che ti abbiamo linkato. Riporteremo quotidianamente tutti i nostri articoli sulla norma)
PER SAPERNE DI PIU':
Tutti gli articoli sulla lean manufacturing pubblicati su QualitiAmoTutti gli articoli sulla ISO 9001 pubblicati su QualitiAmo
La ISO 9001:2015
La ISO 9001