ISO 9001: COSA FARE CON UN LOTTO DI PRODOTTI NON CONFORMI?
Un problema pratico per qualsiasi quality manager: come gestire secondo la ISO 9001 un lotto di prodotti non conformi?
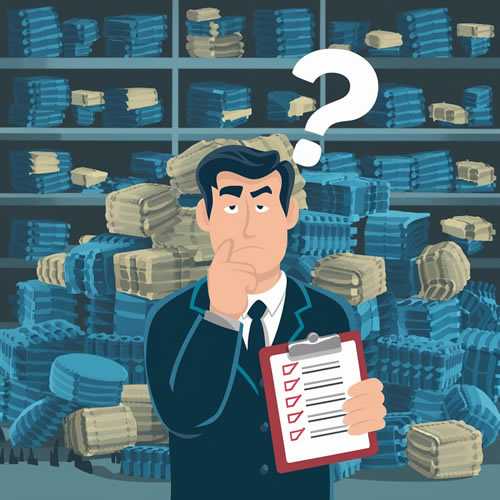
"La qualità è gratuita. Non è un dono, ma è gratuita. Sono le cose 'non di qualità' che costano soldi"
(Philip Crosby)
Per affrontare un problema pratico come quello di un lotto di prodotti non conformi alle specifiche richieste dal cliente, bisogna che i quality manager seguano alcuni passaggi ben precisi. Vediamoli insieme.
1. Identificazione del problema:
- Raccogliere informazioni dettagliate sulla non conformità riscontrata (tipo di difetto, entità, numero di pezzi interessati)
- Verificare le specifiche richieste dal cliente e confrontarle con le caratteristiche del lotto non conforme. Questa analisi comparativa è fondamentale per comprendere la natura e l'entità dello scostamento rispetto ai requisiti del cliente e per definire le azioni necessarie per ripristinare la conformità.
Per verificare le specifiche del cliente, il quality manager deve recuperare la documentazione relativa alle specifiche del prodotto concordate con il cliente (disegni tecnici, schede tecniche, capitolati, contratti, ecc.) ed estrapolare le caratteristiche che il prodotto deve possedere per soddisfare le esigenze e le aspettative del cliente (dimensioni, tolleranze, materiali, prestazioni funzionali, aspetto estetico, ecc.)
Una volta raccolte le specifiche del cliente, il quality manager procede con un'analisi approfondita delle caratteristiche del lotto non conforme che può comportare l'ispezione visiva dei prodotti, la misurazione delle dimensioni critiche, l'esecuzione di test funzionali o l'analisi dei dati di processo. L'obiettivo è identificare con precisione gli scostamenti rispetto alle specifiche richieste e quantificare l'entità della non conformità. Durante questa analisi comparativa, è importante considerare non solo i parametri tecnici, ma anche gli aspetti qualitativi e le esigenze specifiche del cliente. Alcune non conformità possono avere un impatto critico sulla funzionalità o sulla sicurezza del prodotto, mentre altre possono essere considerate accettabili dal cliente in base alle sue priorità e alle sue tolleranze.
Sulla base dei risultati dell'analisi comparativa, il quality manager può classificare le non conformità in base alla loro gravità e all'impatto sul cliente. Questa classificazione permette di stabilire le priorità e di definire le azioni correttive più appropriate per ciascun tipo di non conformità, tenendo conto dei costi, dei tempi di consegna e delle esigenze del cliente. Inoltre, l'analisi comparativa può fornire indicazioni preziose sulle possibili cause della non conformità, come errori di progettazione, problemi di processo, difetti dei materiali o carenze nella formazione degli operatori. Queste informazioni sono fondamentali per l'identificazione delle cause alla radice del problema e per la definizione di azioni preventive efficaci.
2. Contenimento del problema:
- Una volta identificata la non conformità del lotto di prodotti rispetto alle specifiche richieste dal cliente, è fondamentale agire tempestivamente per contenere il problema e prevenire ulteriori danni. Il primo passo è isolare immediatamente il lotto non conforme, al fine di evitare che venga spedito al cliente o utilizzato nella produzione. L'isolamento del lotto non conforme prevede la sua separazione fisica dal resto dei prodotti conformi, attraverso l'identificazione chiara e visibile dei pezzi interessati dalla non conformità. Questo può essere fatto utilizzando etichette, cartellini o altri sistemi di segnalazione che indichino chiaramente lo stato di non conformità del lotto e la necessità di bloccarne l'utilizzo. È importante che l'isolamento del lotto non conforme avvenga in un'area dedicata e controllata, come un'area di quarantena o un magazzino separato, per evitare che i prodotti non conformi possano essere accidentalmente prelevati o confusi con i prodotti conformi. L'accesso a quest'area deve essere limitato al personale autorizzato e adeguatamente formato sulla gestione delle non conformità.
Oltre all'isolamento fisico, è fondamentale bloccare il lotto non conforme anche nei sistemi informatici di gestione della produzione e della logistica. Questo può comportare l'inserimento di un blocco nel sistema ERP (Enterprise Resource Planning) o nel software di gestione del magazzino, per impedire che il lotto non conforme venga prelevato, lavorato o spedito per errore.
L'isolamento tempestivo del lotto non conforme è essenziale per minimizzare l'impatto della non conformità sul cliente e sull'azienda stessa. Impedendo che i prodotti non conformi vengano ulteriormente lavorati o spediti, si evitano sprechi di risorse, si riducono i costi associati alla gestione dei reclami e dei resi, e si preserva la reputazione dell'azienda in termini di qualità e affidabilità. Inoltre, l'isolamento del lotto non conforme permette di avviare rapidamente le attività di analisi delle cause e di definizione delle azioni correttive, senza il rischio di contaminare altri lotti di produzione o di generare ulteriori non conformità. In questo modo, il quality manager può concentrarsi sulla risoluzione del problema alla radice e sul ripristino della conformità del prodotto, minimizzando l'impatto sulla soddisfazione del cliente e sulle performance aziendali.
- Informare tutti i reparti coinvolti (produzione, logistica, vendite) della non conformità e delle azioni di contenimento intraprese. Questa comunicazione trasparente e tempestiva è essenziale per garantire un approccio coordinato e coerente nella gestione del problema e per minimizzare l'impatto negativo sulla soddisfazione del cliente e sulle performance aziendali.
Il quality manager deve preparare una comunicazione chiara e dettagliata, che includa informazioni sulla natura della non conformità, sul lotto di prodotti interessato, sulle azioni di contenimento già intraprese (come l'isolamento del lotto) e sulle eventuali restrizioni o precauzioni da adottare nella gestione del prodotto non conforme. Questa comunicazione può essere diffusa attraverso diversi canali, come e-mail, riunioni di coordinamento o avvisi sul sistema di gestione della qualità.
Il coinvolgimento del reparto produzione è fondamentale per garantire che il processo produttivo sia adeguato alle azioni correttive necessarie per ripristinare la conformità del prodotto. Il quality manager deve informare il responsabile della produzione sulla non conformità riscontrata e sulle possibili cause, in modo che possano essere intraprese le azioni necessarie per correggere il problema e prevenire il ripetersi della non conformità in futuro.
Il reparto logistico deve essere informato dell'isolamento del lotto non conforme e delle restrizioni nella movimentazione e nella spedizione dei prodotti interessati. Questo è essenziale per evitare che il lotto non conforme venga accidentalmente prelevato o spedito al cliente, causando ulteriori problemi e danni alla reputazione dell'azienda.
Infine, il reparto vendite deve essere informato della non conformità e delle azioni intraprese per gestirla, in modo da poter comunicare in modo trasparente con il cliente e gestire eventuali richieste o reclami. Il quality manager deve fornire al reparto vendite le informazioni necessarie per rassicurare il cliente sull'impegno dell'azienda nel risolvere il problema e nel garantire la qualità del prodotto.
3. Analisi delle cause:
- Avviare un'indagine approfondita per identificare le cause alla radice della non conformità. L'analisi delle cause è un passaggio fondamentale per comprendere i fattori che hanno portato alla deviazione dalle specifiche richieste dal cliente e per definire azioni correttive e preventive efficaci.
L'indagine sulle cause della non conformità deve essere condotta in modo strutturato e sistematico, utilizzando metodologie e strumenti di problem-solving riconosciuti, come il diagramma di Ishikawa (o diagramma causa-effetto), l'analisi dei 5 Perché o l'FMEA (Failure Mode and Effects Analysis). Questi strumenti permettono di esplorare in modo approfondito le possibili cause della non conformità, considerando diverse categorie di fattori, come materiali, metodi, macchine, manodopera e ambiente.
Per condurre un'analisi delle cause efficace, il quality manager deve coinvolgere un team multifunzionale, composto da esperti provenienti da diverse aree aziendali, come la produzione, l'ingegneria di processo, la qualità e la logistica. Questo approccio cross-funzionale permette di raccogliere diverse prospettive e competenze, favorendo una comprensione più completa del problema. Il team di analisi delle cause deve iniziare raccogliendo e analizzando tutti i dati e le informazioni disponibili sulla non conformità, come i rapporti di ispezione, i dati di processo, le specifiche tecniche e i feedback dei clienti. Questi dati devono essere esaminati in modo critico per identificare eventuali pattern, tendenze o anomalie che possano fornire indizi sulle cause del problema.
Successivamente, il team deve condurre un'analisi approfondita del processo produttivo, esaminando ogni fase e attività per identificare potenziali punti di debolezza o di variabilità che possano aver contribuito alla non conformità. Questo può comportare l'osservazione diretta del processo, l'intervista degli operatori e l'analisi dei parametri di processo e delle procedure operative. Attraverso l'applicazione degli strumenti di problem-solving e l'analisi dei dati raccolti, il team può generare una lista di potenziali cause della non conformità, classificandole in base alla loro probabilità e al loro impatto. Le cause più probabili e significative devono essere ulteriormente investigate e validate attraverso test, esperimenti o analisi aggiuntive.
Una volta identificate le cause alla radice della non conformità, il team può definire le azioni correttive e preventive più appropriate per eliminare il problema alla fonte e prevenirne il ripetersi in futuro. Queste azioni possono includere modifiche al processo produttivo, aggiornamenti delle procedure, formazione del personale o miglioramenti dei controlli di qualità.
- Coinvolgere un team multifunzionale (qualità, produzione, ingegneria) nell'analisi delle cause.
Come abbiamo detto, il coinvolgimento di un team multifunzionale nell'analisi delle cause di una non conformità è un elemento chiave per un'indagine approfondita ed efficace. Il team multifunzionale deve essere composto da membri con conoscenze specifiche e complementari, in grado di contribuire in modo significativo all'identificazione delle cause alla radice della non conformità. Il responsabile della qualità porta la sua expertise nella gestione dei sistemi di qualità, nelle metodologie di problem-solving e nell'analisi dei dati. Il responsabile della produzione fornisce una conoscenza approfondita del processo produttivo, delle procedure operative e delle potenziali fonti di varianza. L'ingegnere di processo contribuisce con le sue competenze tecniche sulla progettazione del prodotto, sui materiali e sulle tecnologie di produzione.
Questo approccio cross-funzionale permette di affrontare il problema della non conformità da diverse angolazioni, considerando tutti i possibili fattori che possono aver contribuito alla deviazione dalle specifiche richieste. Ogni membro del team porta un bagaglio di conoscenze ed esperienze uniche, che possono aiutare a identificare cause nascoste o interconnessioni tra diversi aspetti del processo produttivo.
Durante l'analisi delle cause, il team multifunzionale deve adottare un approccio strutturato e basato sui dati. Utilizzando strumenti di problem-solving il team può esplorare sistematicamente le diverse categorie di cause potenziali, come materiali, metodi, macchine, manodopera e ambiente. Ogni membro del team contribuisce ad analizzare in profondità ciascuna categoria e a identificare le cause più probabili e significative.
- Utilizzare strumenti di problem-solving per individuare le cause primarie.
Durante l'analisi delle cause di una non conformità, come abbiamo detto, l'utilizzo di strumenti di problem-solving consolidati è fondamentale per individuare in modo sistematico e approfondito le cause primarie del problema. Questi strumenti permettono al team multifunzionale di esplorare tutte le possibili fonti di variabilità e di identificare le relazioni causa-effetto che hanno portato alla deviazione dalle specifiche richieste.
- Il diagramma di Ishikawa, noto anche come diagramma causa-effetto o diagramma a lisca di pesce, è uno strumento grafico che aiuta a visualizzare in modo strutturato le diverse categorie di cause potenziali che possono aver contribuito al problema. Il diagramma si compone di una linea centrale che rappresenta l'effetto (la non conformità) e di diverse ramificazioni che rappresentano le principali categorie di cause, come materiali, metodi, macchine, manodopera e ambiente.
Durante una sessione di brainstorming, il team utilizza il diagramma di Ishikawa per generare e organizzare le possibili cause della non conformità. Ogni membro del team contribuisce con la sua conoscenza specifica a identificare i fattori che possono aver influenzato il processo produttivo e causato la deviazione. Le cause vengono annotate sotto ciascuna categoria principale, creando una rappresentazione visiva completa delle potenziali fonti di varianza -
Dopo aver compilato il diagramma di Ishikawa, il team può utilizzare la tecnica dei 5 Whys per approfondire ulteriormente l'analisi e individuare le cause primarie del problema. I 5 Perché consistono nel chiedere ripetutamente "Perché?" per ogni causa identificata, fino a raggiungere la radice del problema. Questa tecnica permette di andare oltre i sintomi superficiali e di esplorare le relazioni causa-effetto nascoste.
Ad esempio, se una causa identificata nel diagramma di Ishikawa è "Errore dell'operatore", il team può utilizzare i 5 Whys per approfondire:- 1. Perché l'operatore ha commesso l'errore?
Risposta: Perché non ha seguito la procedura corretta -
2. Perché l'operatore non ha seguito la procedura corretta?
Risposta: Perché non era adeguatamente formato sulla procedura - 3. Perché l'operatore non era adeguatamente formato?
Risposta: Perché il programma di formazione non era aggiornato - 4. Perché il programma di formazione non era aggiornato?
Risposta: Perché non c'era un processo di revisione e aggiornamento regolare - 5. Perché non c'era un processo di revisione e aggiornamento regolare?
Risposta: Perché la direzione non aveva assegnato risorse sufficienti per la formazione
- 1. Perché l'operatore ha commesso l'errore?
- Una volta individuate le cause primarie attraverso il diagramma di Ishikawa e i 5 Whys, il team può definire azioni correttive e preventive mirate per affrontare il problema alla radice. Queste azioni possono includere modifiche al processo, aggiornamenti delle procedure, miglioramenti nella formazione del personale o ottimizzazione delle risorse
- Il diagramma di Ishikawa, noto anche come diagramma causa-effetto o diagramma a lisca di pesce, è uno strumento grafico che aiuta a visualizzare in modo strutturato le diverse categorie di cause potenziali che possono aver contribuito al problema. Il diagramma si compone di una linea centrale che rappresenta l'effetto (la non conformità) e di diverse ramificazioni che rappresentano le principali categorie di cause, come materiali, metodi, macchine, manodopera e ambiente.
4. Azioni correttive:
- Una volta identificate le cause primarie della non conformità attraverso l'analisi approfondita condotta dal team multifunzionale, il passaggio successivo consiste nel definire e implementare azioni correttive immediate per risolvere il problema e ripristinare la conformità del prodotto alle specifiche richieste dal cliente. Le azioni correttive sono interventi mirati volti a eliminare le cause alla radice della non conformità e a prevenirne il ripetersi in futuro. Il team multifunzionale, guidato dal quality manager, deve sviluppare un piano d'azione dettagliato che definisca chiaramente le azioni correttive da intraprendere, le responsabilità assegnate a ciascun membro del team e le tempistiche per l'implementazione. Il piano d'azione deve essere basato sulle cause primarie identificate durante l'analisi e deve affrontare in modo completo e sistematico tutti i fattori che hanno contribuito alla non conformità
- Verificare l'efficacia delle azioni correttive attraverso controlli e test aggiuntivi
- Documentare le azioni correttive intraprese e aggiornarle nel sistema di gestione della qualità
5. Comunicazione con il cliente:
- Informare tempestivamente il cliente della non conformità riscontrata e delle azioni intraprese per risolverla. Una comunicazione trasparente e proattiva con il cliente dimostra l'impegno dell'azienda verso la qualità e la soddisfazione del cliente, contribuendo a mantenere la fiducia e a rafforzare la relazione commerciale.
Non appena il team multifunzionale ha identificato la non conformità e avviato le azioni di contenimento, il quality manager deve contattare il cliente per informarlo della situazione. La comunicazione deve essere chiara, diretta e professionale, fornendo al cliente tutte le informazioni rilevanti sulla natura del problema, sul lotto di prodotti interessato e sulle potenziali implicazioni per il cliente stesso.
Durante la comunicazione iniziale, il quality manager deve rassicurare il cliente che l'azienda sta prendendo il problema molto seriamente e che sono state avviate azioni immediate per contenere la non conformità e prevenire ulteriori impatti negativi. È importante sottolineare che l'azienda si assume la piena responsabilità del problema e che si impegna a risolverlo nel modo più rapido ed efficace possibile.
Oltre a informare il cliente della non conformità, il quality manager deve fornire dettagli sulle azioni correttive che sono state definite e che verranno implementate per risolvere il problema alla radice. Il cliente deve essere messo al corrente del piano d'azione, delle tempistiche previste per la risoluzione e dei progressi compiuti lungo il percorso. È fondamentale mantenere una comunicazione regolare e aggiornata con il cliente durante tutto il processo di risoluzione della non conformità.
Una volta che la non conformità è stata risolta e la conformità del prodotto è stata ripristinata, il quality manager deve comunicare formalmente al cliente la chiusura del problema. Questa comunicazione deve includere un riepilogo delle azioni correttive implementate, dei risultati ottenuti e delle misure preventive messe in atto per evitare il ripetersi del problema in futuro. Inoltre, è opportuno ringraziare il cliente per la sua pazienza e collaborazione durante il processo di risoluzione.
- Fornire al cliente un piano d'azione dettagliato, inclusi i tempi previsti per la risoluzione del problema. Come abbiamo detto, fornire al cliente un piano d'azione dettagliato, inclusi i tempi previsti per la risoluzione del problema, è un elemento chiave nella comunicazione efficace durante la gestione di una non conformità. Un piano d'azione ben strutturato dimostra la professionalità e la competenza dell'azienda nell'affrontare il problema, rassicurando il cliente che sono state intraprese azioni concrete per ripristinare la conformità del prodotto.
Per ogni azione correttiva, il piano d'azione deve specificare chiaramente:
- La descrizione dettagliata dell'azione da intraprendere
- Il responsabile dell'implementazione dell'azione
- Le risorse necessarie per l'implementazione (ad esempio, budget, attrezzature, personale)
- I tempi previsti per l'implementazione, inclusi i traguardi intermedi e la data di completamento
- I criteri di successo per valutare l'efficacia dell'azione correttiva
Inoltre, il piano d'azione deve includere una timeline complessiva che mostri la sequenza e l'interdipendenza delle diverse azioni correttive, fornendo al cliente una chiara visione d'insieme del percorso verso la risoluzione del problema.
Nel presentare il piano d'azione al cliente, il quality manager deve fornire una spiegazione chiara e concisa di ciascuna azione correttiva, sottolineando come queste azioni affronteranno le cause primarie della non conformità e contribuiranno a ripristinare la conformità del prodotto. È importante comunicare al cliente che il piano d'azione è stato sviluppato in modo approfondito e che tiene conto di tutti i fattori rilevanti per una risoluzione efficace del problema.
I tempi previsti per la risoluzione del problema devono essere realistici tenendo conto della complessità delle azioni correttive e delle risorse disponibili. Il quality manager deve essere trasparente riguardo alle tempistiche, comunicando al cliente eventuali incertezze o potenziali ostacoli che potrebbero influenzare i tempi di risoluzione. Allo stesso tempo, è importante dimostrare l'impegno dell'azienda a lavorare in modo diligente ed efficiente per rispettare le scadenze concordate.
Nel caso in cui si verifichino ritardi o imprevisti durante l'implementazione del piano d'azione, è fondamentale comunicare prontamente al cliente le ragioni del ritardo e le azioni intraprese per mitigarne l'impatto. Il quality manager deve lavorare a stretto contatto con il team multifunzionale per identificare soluzioni alternative e per rivedere il piano d'azione in modo da garantire il raggiungimento degli obiettivi di risoluzione del problema.
6. Azioni preventive:
- Identificare le opportunità di miglioramento nel processo produttivo per prevenire il ripetersi della non conformità
- Implementare azioni preventive a lungo termine, come l'aggiornamento delle procedure, la formazione del personale o il miglioramento dei controlli di qualità
- Monitorare l'efficacia delle azioni preventive nel tempo e apportare le necessarie modifiche
7. Gestione del lotto non conforme:
- Valutare le opzioni per la gestione del lotto non conforme (rilavorazione, selezione, rottamazione)
Una volta contenuto il problema, informati i clienti e avviate le azioni correttive, il quality manager e il team multifunzionale devono valutare attentamente le opzioni per la gestione del lotto di prodotti non conformi. La scelta dell'approccio più appropriato dipende da diversi fattori, tra cui la natura e la gravità della non conformità, i requisiti del cliente, i costi associati e l'impatto sulla produzione.
Le tre principali opzioni per la gestione di un lotto non conforme sono:
- Rilavorazione: questa opzione prevede la correzione dei prodotti non conformi per renderli conformi alle specifiche richieste. La rilavorazione può comportare la riparazione, la modifica o il completamento dei prodotti, utilizzando procedure e risorse aggiuntive.
Questa scelta è appropriata quando la non conformità può essere corretta in modo efficace ed efficiente, senza compromettere la qualità o la sicurezza del prodotto. Tuttavia, la rilavorazione può richiedere tempo e risorse significativi, e deve essere attentamente valutata in termini di costi e benefici - Selezione: in alcuni casi, potrebbe essere possibile selezionare i prodotti conformi da un lotto non conforme, separandoli da quelli non conformi. Questa opzione è applicabile quando la non conformità è limitata a una parte specifica del lotto e quando i prodotti conformi possono essere identificati in modo affidabile attraverso ispezioni o test aggiuntivi. La selezione può consentire di recuperare una parte del lotto, riducendo gli sprechi e i costi associati. Tuttavia, richiede un processo di ispezione rigoroso e può comunque comportare la perdita di una parte dei prodotti
- Rottamazione: quando la non conformità è grave e non può essere corretta in modo economicamente vantaggioso, o quando i prodotti non possono essere selezionati in modo affidabile, l'opzione della rottamazione può essere la scelta più appropriata. La rottamazione comporta l'eliminazione completa del lotto non conforme, smaltendo i prodotti in modo sicuro e responsabile. Questa opzione può essere costosa in termini di materiali e risorse perse, ma può essere necessaria per evitare rischi per la qualità, la sicurezza o la reputazione dell'azienda.
- Considerazioni legali e normative: in alcuni settori, come quello medico o alimentare, ci possono essere requisiti normativi specifici per la gestione dei lotti non conformi, che devono essere attentamente valutati. Dopo aver considerato tutti questi fattori, il team multifunzionale può prendere una decisione informata.
- Scegliere l'opzione più appropriata in base alla gravità della non conformità, ai costi e ai tempi di consegna
Dopo aver valutato attentamente le opzioni per la gestione del lotto non conforme, il team deve scegliere l'approccio più appropriato in base a tre criteri chiave:
- la gravità della non conformità - se la non conformità è minore e non compromette la funzionalità, la sicurezza o la conformità normativa del prodotto, la rilavorazione potrebbe essere la scelta più adeguata. Tuttavia, se la non conformità è grave e rende il prodotto inutilizzabile o non sicuro, la rottamazione potrebbe essere l'unica opzione praticabile. In casi di non conformità di gravità intermedia, la selezione potrebbe essere considerata se è possibile identificare e separare in modo affidabile i prodotti conformi da quelli non conformi
- i costi associati - il team deve valutare i costi diretti e indiretti di rilavorazione, selezione o rottamazione, tenendo conto dei materiali, della manodopera, delle attrezzature e delle risorse necessarie. Inoltre, devono essere considerati i potenziali costi di mancata qualità come reclami dei clienti, i resi o i danni alla reputazione. L'opzione scelta deve bilanciare i costi immediati con i benefici a lungo termine, cercando di minimizzare l'impatto finanziario complessivo sulla'zienda
- i tempi di consegna - il team deve valutare l'impatto di ciascuna opzione sulla capacità dell'azienda di rispettare le scadenze di consegna concordate con i clienti. La rilavorazione o la selezione possono richiedere tempo aggiuntivo, ritardando potenzialmente le consegne. In alcuni casi, potrebbe essere necessario dare priorità alla velocità di risoluzione del problema rispetto ai costi, optando per la rottamazione per evitare ritardi significativi nelle consegne. La scelta deve tenere conto delle esigenze e delle aspettative dei clienti, cercando di minimizzare i disagi e mantenere la loro soddisfazione.
- Documentare la decisione presa e le azioni intraprese per la gestione del lotto non conforme. Dopo aver scelto l'opzione più appropriata per la gestione del lotto non conforme, è fondamentale documentare in modo dettagliato la decisione presa e le azioni intraprese. Una documentazione completa e accurata è essenziale per garantire la tracciabilità, la trasparenza e l'apprendimento organizzativo, oltre a dimostrare la conformità alle procedure interne e ai requisiti normativi.
8. Chiusura del problema:
- Verificare che tutte le azioni correttive e preventive siano state completate e che il problema sia stato risolto
- Comunicare al cliente la risoluzione del problema e fornire eventuali informazioni aggiuntive richieste
- Documentare la chiusura del problema nel sistema di gestione della qualità e condividere le lezioni apprese con il team
Seguendo questi passaggi, il quality manager può affrontare in modo strutturato ed efficace il problema di un lotto di prodotti non conformi alle specifiche del cliente, minimizzando l'impatto negativo sulla soddisfazione del cliente e sulla reputazione dell'azienda.
-
"La nuova ISO 9001:2015 per riorganizzare, finalmente, l'azienda per processi" - Si aggiunge alla collana dei libri di QualitiAmo il primo testo che svela i segreti della futura norma.
Dalla teoria alla pratica: il secondo lavoro di Stefania Cordiani e Paolo Ruffatti spiega come migliorare la vostra organizzazione applicando la nuova norma attraverso i suggerimenti del loro primo libro
(Vai all'articolo che descrive il nuovo libro)"Organizzazione per processi e pensiero snello - Le PMI alla conquista del mercato" - Da una collaborazione nata sulle nostre pagine, un libro per far uscire le PMI dalla crisi.
L’ideatrice di QualitiAmo e una delle sue firme storiche spiegano come usare con efficacia la Qualità.
(Vai all'articolo che descrive il primo libro)
(Vuoi restare aggiornato gratuitamente sulla ISO 9001:2015? Visita ogni giorno la pagina che ti abbiamo linkato. Riporteremo quotidianamente tutti i nostri articoli sulla norma)
PER SAPERNE DI PIU':
Tutti gli articoli sulla ISO 9001ISO 9001
La ISO 9001:2015
Tutti gli articoli sulla ISO 14001
Tutti gli articoli sulla ISO 45001
Tutti gli articoli sulla ISO 42001
Tutti gli articoli sulla ISO 27001