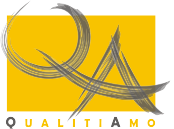 |
Il forum sulla Qualità di QualitiAmo Torna all'homepage di QualitiAmo
|
Precedente :: Successivo |
Autore |
Messaggio |
Federik Nuova recluta del forum
Registrato: 03/01/16 13:57 Messaggi: 4
|
Inviato: Ven Gen 08, 2016 3:20 pm Oggetto: come impostare interventi lean e six sigma su caso aziendale |
|
|
Buongiorno a tutti
Sto facendo una tesi sulla lean production e la metodologia six sigma.
Come caso applicativo mi trovo davanti ad un’azienda metalmeccanica che produce oltre 3000 diversi codici di prodotto, l’80% dei quali su disegno del cliente.
Sostanzialmente si tratta di fare un po’ di brainstorming su quali interventi fare in ottica di miglioramento della produttività. Dal canto mio mi sono formato su vari libri e risorse web per quanto riguarda la teoria, ma non ho nessuna esperienza pratica in aziende reali, quindi sono qui a chiedervi suggerimenti.
Per ora ho pensato un po’ a come applicare la lean production a questo caso…
La teoria lean suggerisce di cercare di convertire l’organizzazione per funzioni in organizzazione per processi e dividere i codici in famiglie di prodotti in ottica group technology (cioè col 70-80% di processi in comune), fare la value stream map per ogni famiglia ed idealmente creare delle celle di lavoro dedicate (con macchinari e team dedicati) in modo da minimizzare le distanze tra i processi e favorire il flusso continuo.
La prima difficoltà che trovo nel fare questo sta nel numero di codici: nella teoria si fanno sempre casi limite per semplicità per far capire il meccanismo, ok, ma dividere in famiglie 10 codici e dividerne 3000+ fa una bella differenza.
In primis non saprei come affrontare il raggruppamento. Farlo a mano mi sembra ben poco fattibile. Conoscete software o altri metodi per fare ciò?
In seconda battuta, in funzione della numerosità di ciascuna famiglia, mi troverei con due possibili risultati:
1) Tantissime celle, in ognuna delle quali si producono relativamente pochi codici: diventa un problema in quanto servirebbero molti macchinari “doppioni”, anche se di capacità produttiva non altissima, per rendere complete le celle (attualmente invece ci sono poche macchine ad alta capacità produttiva, e proporre la dismissione delle macchine vecchie per sostituirle con nuove più flessibili non è fattibile nel breve per via dei costi)
2) Relativamente poche celle, in ognuna delle quali si producono tantissimi codici: quindi sarebbe come convertire un’organizzazione per funzioni in una sempre per funzioni ma con reparti un po’ più piccoli. Coordinare tutte le interdipendenze con kanban e fare livellamento diventerebbe un delirio. Considerando che se i codici nella stessa cella sono molti, difficilmente si avrebbero tempi di processo uniformi e il bilanciamento delle linee diventerebbe arduo.
Oppure è proprio meglio cambiare approccio e indirizzare le azioni su qualcos’altro (sempre in ottica lean)?
Per la parte six sigma pensavo poi di fare: misura della capability di un processo per uno specifico prodotto, fare un DOE (se in azienda me lo permettono), ricalcolo della nuova capability e fase di controllo con carte di controllo.
Avete qualche consiglio su come impostare il lavoro?
Grazie fin d’ora per qualsiasi suggerimento,
Federico |
|
Top |
|
 |
|
 |
Paoloruffatti Yoda
Registrato: 26/07/08 11:05 Messaggi: 4071
|
Inviato: Ven Gen 29, 2016 5:24 pm Oggetto: |
|
|
Ciao Federico,
mi sono trovato alcune volte in situazioni anche peggiori, come nel caso di una ditta che aveva più o meno lo stesso numero di codici che ci racconti.
Questi facevano catenine d'oro, quindi figurati il tipo di lavoro con un sacco di prodotti che dovevano passare per un forno e saprai che i permessi per le emissioni in atmosfera le USL li concedono a seconda della testa del signore che è preposto a questo "importante compito" e quindi anche spostare i forni per completare le celle di lavorazione era un casino (di duplicarli nemmeno a pensarlo).
Per questa ed altre vicissitudini il titolare aveva chiesto ed ottenuto di fare un nuovo stabilimento (con sicurezze da forte Knox, ovviamente) in un sito vicino anche al secondo stabilimento che avevano già fatto per allargarsi una prima volta dieci anni prima (risultato poi un costo secco inutile, sempre ovviamente)
Questo imprenditore misconosceva il diagramma di Pareto e quidi si stava scervellando per capire a quale delle 3000 e più referenze, sulle oltre cento linee di prodotto dovesse dedicare del tempo per fare la scelta di cui sopra (da fare nel nuovo stabilimento).
Questo imprenditore [aveva ascoltato anche lui l'Unione Industriali locale che gli aveva venduto un corso Lean da applicare alla sua produzione [di per sè già una vaccata....e se vuoi ne parliamo più serenamente da un'altra parte (hai visto che c'è il modo di dirci le cose privatamente): mi dispiace per la tua tesi, ma purtroppo chi te l'ha data non ha la più lontana idea di che cosa sia davvero la lean production, o peggio, il lean Thinking specie se applicato male].
Tornando al tuo caso io applicherei tutta la tua tesi al 20% dei codici che costituisce la classe "A" 3000X20%=600 codici, cosa ben più potabile, poi se vai a dividerli davvero per linee di prodotto vedrai che il tuo studio interesserà di nuovo un altro 20% di linee, che significa che tu ti dovrai ristudiare i lay out di un numero bassissimo di linee di prodotto (nel mio caso si riducevano a 19, di cui solo 10 erano interessate al passaggio intermedio in forno.
Per dirti come andò a finire io gli feci cancellare la costruzione del nuovo stabilimento (e dissi di festeggiare l'evento con una crociera!) e spostare il forno solo di qualche metro così che potesse servire le 10 linee con spostamenti brevi dei "carrelli" dagli spazi ad "U" di produzione.
Insegnai loro di fare il "livellamento di produzione", facendogli vedere che si potevano accorciare i tempi di consegna di circa il 50% (il che, anche solo finanziariamente, trattandosi di ORO, non guastava affatto.
Non mi disse nemmeno "can bestia, Grazie"...mi pagò le mie fatture e amen.
..... Non so se è andato in crociera lui e sua moglie!
Sempre tornando al tuo caso, guarda che il lean thinking, che andava bene per costruire aeromobili in grandi stabilimenti americani (c'è un bell'esempio in internet) è ideologicamente una ciofeca. Solo cercando di togliere le inefficienze nell'organizzazione del lavoro (....e non sodomizzando gli operai perchè lavorino di più) si ottengono risultati seri e poi il Lean Thinking purtroppo è pensato per applicare questi principi all'interno di tante "funzioni" anzichè ai "processi di attraversamento"!, perchè le maggiori inefficienze nascono e si sviluppano nel passaggio da una funzione (o Silo) ad un'altra e quasi mai all'interno di ogni funzione.
Poi ti dirò l'altro grossissimo limite del Lean Thinking applicato qui da noi:
Se tenti di applicarlo facendo capire al personale che è un metodo calato dall'alto STAI SICURO che sarà un fiasco sesquipedale! perchè gli operatori che lo vedono lo rigettano; loro pensano, infatti, che sia la solita genialata inventata dal capo per farli lavorare di più e non ci sono ne santi ne altro che possano farli recedere da questa idea! Ricordatelo in vita!
Scoprirai inoltre che lo scoramento che ti ha preso per le macchine da proporre per una sostituzione è sbagliato perchè riguarderà una o due macchine veramente (affermo questo perchè vedrai che se non sei dentro ad uno stabilimento catorcio con tutte le macchine da buttare in barilone, i capi officina, che hanno Pareto nel sangue, avranno già chiesto ed ottenuto di sostituire i catorci con le poche macchine che servono veramente (e non chiedere al titolare se sa qualcosa di "capability" di macchina perchè ti chederà se è roba che si mangia e poi dirà che gli alti scarti che escono dai catorci sono dovuti all'operatore che pensa alla morosa anzichè lavorare seriamente). Mentre si arabbatteranno ogni volta (tirando di quelle saracche che fanno chiaro) ad usare ogni tanto tempo i catorci rimasti, per fare i prodotti di classe "C", ma per una-due volte all'anno-mese ci possono ancora stare, ... se quello spilorcio che ha la Cayenne fuori della porta non gliele compera nuove.
Ciao
Paolo |
|
Top |
|
 |
|
|
Non puoi inserire nuovi argomenti Non puoi rispondere a nessun argomento Non puoi modificare i tuoi messaggi Non puoi cancellare i tuoi messaggi Non puoi votare nei sondaggi
|
|