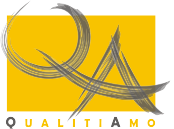 |
Il forum sulla Qualità di QualitiAmo Torna all'homepage di QualitiAmo
|
Precedente :: Successivo |
Autore |
Messaggio |
QualitiAmo - Stefania Moderatore

Registrato: 16/09/07 18:37 Messaggi: 26601
|
Inviato: Gio Lug 30, 2009 10:35 am Oggetto: Perché produzione snella e lean maintenance sono diverse |
|
|
Su ComFy Magazine potete leggere un articolo dal titolo: "Why Lean And Lean Maintenance Are Different".
Questa è la versione tradotta in italiano con il traduttore automatico di Google.
The problem is that the same fundamental principles have been bought directly from the production environment into the asset maintenance environment. The same seven areas of waste, the same initiatives such as just-in-time inventory management, and the same sort of focus on the day-to-day without including a longer term focus.
(In the most extreme cases it appears as if LEAN seems to be a metaphor for every buzzword and service that a consultancy has to offer – but that would be cynical)
“So what?” you say. “Why should maintenance be any different?”The reason why a lean maintenance approach cannot just be a mirror image of a lean production approach is because the business dynamics of asset maintenance and those of production are fundamentally different.
A short summary of the differences is below, but in my new book, tentatively titled Asset Resource Planning: Lean strategies for efficient maintenance, this is explained in a lot more detail.
Production plans are driven by sales forecasts and in the nearer term by sales orders. This means they are driven by an exact schedule of works. Asset maintenance, on the other hand, is driven in part by a schedule of routine work and in part by the likelihood of failure of the assets under management.
This means that initiatives such as JIT inventory management have only a limited ability to assist the efficiency of the maintenance process. Issues such as Just-in-case inventory management are far more important.
This has implications not only within the area of operations, but throughout the entire supply chain. Often the improvement of a supply chain is based on “how we buy”, the probabilistic nature of asset maintenance means also that we need to be thinking about “why we buy”.
Production efficiency is gained almost entirely through present operations. So to be “productive without waste” is thought of in terms of the day-to-day activities involved in managing the production processes. (And rightly so)
In asset maintenance being “productive without waste” has an additional perspective to it, that of time. A large part of any asset maintenance spend over time relates to asset replacement and refurbishment intervals.
Depending on the type of plant these are often very large scale costs on a par with the initial equipment purchase in terms of magnitude.
So “productive without waste” means not replacing these too early, and often in not allowing them to fail completely before they fail. So to be truly efficient we need to control a range of issues related to asset use, type, expected life and other issues.
This is significant and reaches outside of the maintenance function itself. For example; a machine that is subject to regular overload situations is likely to have a shortened life expectancy, meaning that capital will need to be spent on it at an earlier stage than previously thought.
The last issue we will explore here is that of data management and collection. Improvement of production processes can often be made through recording and acting upon dynamic operational information.
In asset maintenance this also has its place, but as we can see from the issue above we also need to be able to confidently forecast spending in the future and how that is affected by current activities.
This requires data other than the dynamic operational data. It also requires static data on equipment type, location and age; as well as a range of data regarding failure rates, asset condition and other areas.
While this seems straight forward, when this task is not correctly managed it can be a tremendous strain on the resources of the asset maintenance department. Particular when they end up spending a lot of time and money collecting data that is of no use to them!
So where does this leave us? If we believe firmly, as I do, that LEAN maintenance needs a different focus that LEAN production, what should it be?
Over the years I have put together a list of eight areas where the majority of waste in maintenance occurs. Again it is difficult to go through it in detail here but hopefully it will give you the picture.
While some of these are the same as those in a standard LEAN approach, there are some notable differences. Some items have been deleted from the list of wasteful activities, while others have been added.
Unproductive work – Efficiently doing work that doesn’t need to be done!
Delays in motion – Waiting times, delays waiting for parts, machinery, people, etcetera
Unnecessary motion – Unneeded travel, trips to tool stores or workshops, looking for items, moving mobile work stations around without good reason.
Poor management of inventory – Not able to have the right parts at the right time. A complex area that can cause many of the other areas of waste on this list.
Rework – Having to repeat tasks, or do additional tasks, as a result of poor workmanship.
Underutilization of people – Using people to the limits of their qualifications, not to the limits of their abilities!
Ineffective data management – Collecting data that is of no use, or failure to collect data which is vital. Both of these are parts of this area.
Misapplication of machinery – Incorrect operation or deliberate operational strategies leading to maintenance work being done when it needn’t be.
This is a topic we could discuss for a long time and it is one that will no doubt cause a lot of disagreement and hopefully some debate. But once you sit down and really look at the business of maintaining assets, how it works and what the important elements are, I believe you will agree with me.
If we really want to deliver “productivity without waste”, or efficiency, in asset maintenance, then we need a different version of LEAN; one that takes into account the unique business dynamics of the area that we work in.
Good luck with your efficiency initiatives! _________________ Stefania - Staff di QualitiAmo
ISO 9001:2015 - SI AGGIUNGE ALLA COLLANA DEI LIBRI DI QUALITIAMO IL NUOVO TESTO CHE SVELA I SEGRETI DELLA FUTURA NORMA
IL PRIMO LIBRO NATO SULLE PAGINE DI QUALITIAMO
HAI DATO UN'OCCHIATA AL REGOLAMENTO DEL FORUM PRIMA DI SCRIVERE IL TUO MESSAGGIO? |
|
Top |
|
 |
|
 |
|
|
Non puoi inserire nuovi argomenti Non puoi rispondere a nessun argomento Non puoi modificare i tuoi messaggi Non puoi cancellare i tuoi messaggi Non puoi votare nei sondaggi
|
|