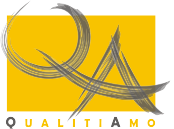 |
Il forum sulla Qualità di QualitiAmo Torna all'homepage di QualitiAmo
|
Precedente :: Successivo |
Autore |
Messaggio |
QualitiAmo - Stefania Moderatore

Registrato: 16/09/07 18:37 Messaggi: 26590
|
Inviato: Mar Lug 28, 2009 2:17 pm Oggetto: Perché i dati sono così critici per il 6Sigma |
|
|
Su Kusna's blog potete leggere un articolo dal titolo: "Why Data is Critical to Six Sigma".
Questa è la versione tradotta in italiano con il traduttore automatico di Google.
Before being introduced to Six Sigma, many managers consider it a mysterious approach to process efficiency that cannot be properly measured. Indeed, there are plenty of business management strategies that emerge and are successful for awhile based upon fad rather than delivering practical results. By contrast, this methodology is firmly grounded in data and statistical analysis.
The foundation of this approach is built upon the collection and evaluation of numbers. Every step of the deployment, from the identification of the initiative’s objective to long-term performance tracking, relies upon numbers. Below, I’ll explain how data is used throughout a Six Sigma assignment.
The Core Of Process Improvement
The purpose of the methodology is to improve business processes. In order to do that, the project team must identify variances and study their individual and collective impacts on waste. The only reliable way to make those improvements is by collecting data and measuring it against existing baselines.
The dedication of Six Sigma initiatives to a quantitative approach not only helps to ensure improvements, but it also sets the stage for ongoing measurement. Every process has a tendency to accrue waste over time. By establishing baselines and measuring future results by them, that waste can be kept at bay. Ultimately, that improves product cycle times, deliverability, and revenue while lowering operational expenses.
Identifying And Eliminating Waste
A Six Sigma project begins with identifying opportunities for an organization to limit waste and variances that exist in a given process. Part of that procedure includes isolating inputs and outputs. Those variables are isolated in order that the project team can collect metrics that might lead to future improvements.
During the assignment, the metrics collected from the inputs and outputs are compared to predefined benchmarks. At this point, the project team has two responsibilities. First, they must identify the presence of defects and errors within the process. Second, they must review the gathered metrics and determine each variable’s impact on Critical To Quality (CTQ) factors.
Note how the metrics are vital to the success of the entire initiative. Without them, the organization’s current performance - and the errors and defects which may exist within - cannot be properly analyzed.
Designing Solutions
The next phase of a Six Sigma initiative relies heavily on the data collected from the previous steps. The project team will develop solutions which, when implemented, will hopefully lead to process-related improvements. These solutions are not designed in a vacuum; they rely upon the gathered metrics.
The project team will review each of the key variables to determine the effects of making changes to them. While there is some experimentation involved, designing solutions which can eliminate waste and variances depends upon rigorous statistical analysis.
Measuring Results
Once the Six Sigma team’s solutions have been implemented, they must be monitored in order to track their success. Data will be collected from each of the inputs and outputs identified earlier in the project to determine whether the solutions are having the intended effect.
It is possible that the project team’s changes will lead to improvements in the process, yet not completely eliminate errors, defects, and waste. This is the reason data is so important to success. The process metrics must be reviewed and analyzed until waste has been eliminated. Then, once that has been accomplished, they must be perpetually monitored to ensure waste does not creep in again.
Those who are familiar with the Six Sigma methodology will not be surprised to hear that data is essential to the success of a project. It both guides the initiative and provides a platform on which to objectively measure results. _________________ Stefania - Staff di QualitiAmo
ISO 9001:2015 - SI AGGIUNGE ALLA COLLANA DEI LIBRI DI QUALITIAMO IL NUOVO TESTO CHE SVELA I SEGRETI DELLA FUTURA NORMA
IL PRIMO LIBRO NATO SULLE PAGINE DI QUALITIAMO
HAI DATO UN'OCCHIATA AL REGOLAMENTO DEL FORUM PRIMA DI SCRIVERE IL TUO MESSAGGIO? |
|
Top |
|
 |
|
 |
|
|
Non puoi inserire nuovi argomenti Non puoi rispondere a nessun argomento Non puoi modificare i tuoi messaggi Non puoi cancellare i tuoi messaggi Non puoi votare nei sondaggi
|
|