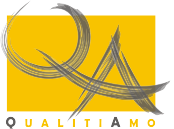 |
Il forum sulla Qualità di QualitiAmo Torna all'homepage di QualitiAmo
|
Precedente :: Successivo |
Autore |
Messaggio |
QualitiAmo - Stefania Moderatore

Registrato: 16/09/07 18:37 Messaggi: 26590
|
Inviato: Lun Lug 27, 2009 4:03 pm Oggetto: TQM - Total Quality Mangement |
|
|
su 108Quality potete leggere un articolo dal titolo: "Total Quality Management".
Questa è la versione tradotta in italiano con il traduttore automatico di Google.
Total Quality Management – TQM is a management strategy aimed at embedding awareness of quality throughout the organization and approach to long-term success through customer satisfaction and continuously improve the business processes.
TQM has been widely used in all different organization, manufacturing, education, government, service industries, as well as NASA space and science programs.
In a TQM effort, all members of an organization participate in improving processes, products, services and the culture in which they work.
The methods for implementing this approach come from the teachings of such quality leaders as Philip B. Crosby, W. Edwards Deming, Armand V. Feigenbaum, Kaoru Ishikawa and Joseph M. Juran.
A core concept in implementing Total Quality Management – TQM is Deming’s 14 points, a set of management practices to help companies increase their quality and productivity:
1. Create constancy of purpose for improving products and services.
2. Adopt the new philosophy.
3. Cease dependence on inspection to achieve quality.
4. End the practice of awarding business on price alone; instead, minimize total cost by working with a single supplier.
5. Improve constantly and forever every process for planning, production and service.
6. Institute training on the job.
7. Adopt and institute leadership.
8. Drive out fear.
9. Break down barriers between staff areas.
10. Eliminate slogans, exhortations and targets for the workforce.
11. Eliminate numerical quotas for the workforce and numerical goals for management.
12. Remove barriers that rob people of pride of workmanship, and eliminate the annual rating or merit system.
13. Institute a vigorous program of education and self-improvement for everyone.
14. Put everybody in the company to work accomplishing the transformation.
In Japan, Total Quality Management – TQM comprises four process steps;
1. Kaizen– Focuses on “Continuous Process Improvement”
2. Atarimae Hinshitsu – The idea that “things will work as they are supposed to”
3. Kansei – Examining the way the user applies the product leads to improvement in the product itself.
4. Miryokuteki Hinshitsu – The idea that “things should have an aesthetic quality”
Total Quality Management – TQM started to appear in the 1980s and there are two theories of its origin:
1. One theory is that Total Quality Management – TQM was created as a misinterpretation from Japanese to English since no difference exists between the words “control” and “management” in Japanese. According to William Golomski (American quality scholar and consultant, 1924-2002) TQM was first mentioned by Koji Kobayashi at NEC (Nippon Electrical Company) in his speech when he received the Deming Prize in 1974.
2. The American Society for Quality says that the term Total Quality Management – TQM was used by the U.S. Naval Air Systems Command in 1984 to describe its Japanese-style management approach to quality improvement since they did not like the word control in Total Quality Control. The word management should then have been suggested by one of the employees, Nancy Warren. This is consistent with the story that the United States Navy Personnel Research and Development Center began researching the use of statistical process control (SPC), the work of Juran, Crosby, and Ishikawa, and the philosophy of W. Edwards Deming to make performance improvements in 1984. This approach was first tested at the North Island Naval Aviation Depot.
The term “Total Quality Management – TQM” has lost favor in the United States in recent years: “Quality Management – QM” is commonly substituted. “Total Quality Management – TQM” however, is still used extensively in Europe. _________________ Stefania - Staff di QualitiAmo
ISO 9001:2015 - SI AGGIUNGE ALLA COLLANA DEI LIBRI DI QUALITIAMO IL NUOVO TESTO CHE SVELA I SEGRETI DELLA FUTURA NORMA
IL PRIMO LIBRO NATO SULLE PAGINE DI QUALITIAMO
HAI DATO UN'OCCHIATA AL REGOLAMENTO DEL FORUM PRIMA DI SCRIVERE IL TUO MESSAGGIO? |
|
Top |
|
 |
|
 |
|
|
Non puoi inserire nuovi argomenti Non puoi rispondere a nessun argomento Non puoi modificare i tuoi messaggi Non puoi cancellare i tuoi messaggi Non puoi votare nei sondaggi
|
|