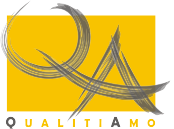 |
Il forum sulla Qualità di QualitiAmo Torna all'homepage di QualitiAmo
|
Precedente :: Successivo |
Autore |
Messaggio |
QualitiAmo - Stefania Moderatore

Registrato: 16/09/07 18:37 Messaggi: 26590
|
Inviato: Lun Lug 20, 2009 11:33 am Oggetto: Ridurre scarti e rilavorazioni |
|
|
Su ThomasNet potete leggere un articolo dal titolo: "Ways to Reduce Scrap and Rework".
Potete tradurre il testo in italiano con il traduttore automatico di Google.
Manufacturers can save time and money by cutting the amount of scrap they produce and limiting rework. Here are some strategies to consider.
One of the ways businesses can cut costs and improve their overall efficiency is by reducing the amount of scrap and rework in their plants. Rework results in lost time and increased work that can't be recouped, while high scrap rates lead to high material costs and lost time making parts that will not bring in revenue.
By effectively managing rework and scrap, companies can save time and money while reducing interruptions to the production cycle, resulting in a higher-quality product.
The first step to reducing rework and scrap is determining the main causes of rework and scrap.
The Infosys-Oracle Blog recommends developing metrics to measure rework in quantifiable terms. Once the metric is determined, companies must collect the data related to rework per the metrics used. "Proper analysis of the collected data (statistical and empirical), would lead to identification of the main causes of rework," the Infosys-Oracle Blog says. "These analyses identify the process, machines or resources that mostly induce the rework."
A similar analysis is required to ascertain the main causes of scrap. Once the causes are determined, the company can then take action to reduce scrap by implementing automated quality checks of raw materials and plant processes, among others.
Aberdeen Group (membership required) suggests companies prevent scrap and rework during the design phase. Simulation is one strategy that helped the companies in Aberdeen's research to have fewer change orders (36 percent) after releasing the design to manufacturing. It also helped them reduce the amount of physical prototypes, which are eventually scrapped, by 37 percent.
"Physical prototyping is a necessary part of product development, but the fewer prototypes required, the better," adds Parametric Technology Corp. (PTC). Weeks of development time can be cut by reducing the number of physical prototypes used for testing. Rather than using physical prototypes, PTC also recommends virtual prototyping and simulation for much of the testing.
"Full-digital product representation lets you replace some physical prototypes with virtual prototypes," PTC says. "Full-digital also means — depending on your 3D CAD software — you can "shrink-wrap" your 3-D model to a smaller, more manageable size, and e-mail it to remote members of the design or manufacturing team, thus saving significant time and cost."
Additionally, sharing information between the designers and manufacturers allows both sides to identify potential problems before they start. Collaboration between engineering and manufacturing enables both sides to check for manufacturability. If the products are not manufacturable, they end up as scrap or something that needs to be reworked.
By sharing design information from the start, manufacturers can point out potential production problems while the design engineers are working on the product, allowing them to correct the product then and avoid finding product deficiencies later, Aberdeen explains.
Both getting the product right at the get-go and focusing on continuous improvement are imperative to reducing rework and scrap. Aberdeen notes:
Those manufacturers most satisfied with the amount of scrap and rework they produce focus on improving the quality of simulations by tracking the problems identified in the test lab that could have been identified earlier in a simulation. This enables them to learn from experience and effectively improve the quality of future simulations. In addition, these manufacturers identify and track the root cause of scrap and rework, which again, allows them to learn from past mistakes and enables them to make corrections to future product designs to avoid a re-occurrence of the same problem.
A final step is applying lean manufacturing and Six Sigma principles to the manufacturing process eliminates waste and thus reduces the risk of scrap, Aberdeen adds. According to a June poll by Medical Edge, 79 percent of respondents said their companies practiced lean manufacturing as a way to wring out waste from the manufacturing stream.
How is your company cutting out scrap and reducing rework? _________________ Stefania - Staff di QualitiAmo
ISO 9001:2015 - SI AGGIUNGE ALLA COLLANA DEI LIBRI DI QUALITIAMO IL NUOVO TESTO CHE SVELA I SEGRETI DELLA FUTURA NORMA
IL PRIMO LIBRO NATO SULLE PAGINE DI QUALITIAMO
HAI DATO UN'OCCHIATA AL REGOLAMENTO DEL FORUM PRIMA DI SCRIVERE IL TUO MESSAGGIO? |
|
Top |
|
 |
|
 |
|
|
Non puoi inserire nuovi argomenti Non puoi rispondere a nessun argomento Non puoi modificare i tuoi messaggi Non puoi cancellare i tuoi messaggi Non puoi votare nei sondaggi
|
|