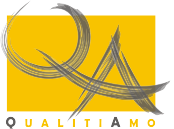 |
Il forum sulla Qualità di QualitiAmo Torna all'homepage di QualitiAmo
|
Precedente :: Successivo |
Autore |
Messaggio |
QualitiAmo - Stefania Moderatore

Registrato: 16/09/07 18:37 Messaggi: 26595
|
Inviato: Mer Ago 26, 2009 10:52 am Oggetto: Comprendere e implementare i 7 flussi della produzione |
|
|
Su Reliable Plant potete leggere un articolo dal titolo: "Understand and implement the 7 flows of manufacturing".
Questa è la versione tradotta in italiano con il traduttore automatico di Google.
“All problems can be solved by looking at and understanding the seven flows.” – Chihiro Nakao
In the book Lean Thinking, authors James Womack and Daniel Jones outlined lean thinking in terms of focusing on clearly specifying “value”, lining up all the value-creating activities along a “value stream”, making value “flow” smoothly at the “pull” of the customer in pursuit of “perfection”. Following these deceptively simple concepts, many of us struggle on the path to becoming lean as we constantly get stuck in the muck of waste, status quo and egocentric leadership.
Let’s look at just the concept of flow. It’s sounds easy enough to understand, right? Most of us know what is meant by flow and what is not flow. Flow is going down the highway at full speed with little or no traffic whereas getting stuck in a bumper-to-bumper traffic jam is not flow.
But how do we make value “flow” smoothly?
Many years ago, I was taught by one of my Japanese sensei, Nakao-san, the seven flows in manufacturing. These include:
1. The flow of raw material
2. The flow of work-in-process
3. The flow of finished goods
4. The flow of operators
5. The flow of machines
6. The flow of information
7. The flow of engineering
We must first observe each of these flows to gain full understanding. In our observation, take notes and sketch out the seven flows as we see them. It is very important not to skip this step and actually sketch out the seven flows regardless of our artistic skills. Why do you think it is important for us to sketch them?
As we are sketching the seven flows, what are some of the things we should be observing?
To help us think more of flow, here are just a few things to look for while in gemba.
Raw Material, WIP and Finished Goods Flow
What is the standard work? What are the locations and distances? What are the container types and sizes? What are the packaging materials and what do we do with it? Are there any machine cycle times? How is the transfer of material accomplished? What are the conveyors, carts, forklifts being used?
Operator Flow
What is the standard work and operator’s cycle time (determine pace of the line, slowest to fastest)? What are the operator’s body movements … arms, hands, head, eyes, legs and feet? Observe the “go-gets” of operators getting things to do their tasks.
Machine Flow
What is the machine cycle time? What are the set-up requirements? What is the machine process and is it right-sized only for what is required? Are there unused features in the machine? What steps are required to operate the machine? What are the requirements of properly maintaining the machines? Are the machines purchased or built in-house? Observe the machine wastes (collection, disposal, size and shape, recycle coolant, etc.).
Information Flow
Observe the transfer of information. What information is needed? What is the path of information? What are the decisions made by the operator? How many decisions are made by the operator? What does the operator do when a problem occurs or if he or she has a question? How does information of problems get passed on? Who responds to the operator’s needs? What information is on production control boards, production schedules, kanbans, manufacturing plans, etc.?
Engineering Flow
What is the tooling required? What are the process controls and quality checks? Are there “go/no-go” gauges? Observe any hanedashi devices (the mechanisms to automatically eject a part from the machine to free up the operator to only load the machine).
Can you think of other items in observing the seven flows?
In each of the seven flows, observe the stops, the hesitations, the delays, the re-dos. We should also consider all seven flows working in harmony to improve flow. From these detailed observations of the seven flows and our gained understanding of the process, we will see how to make value flow smoothly. _________________ Stefania - Staff di QualitiAmo
ISO 9001:2015 - SI AGGIUNGE ALLA COLLANA DEI LIBRI DI QUALITIAMO IL NUOVO TESTO CHE SVELA I SEGRETI DELLA FUTURA NORMA
IL PRIMO LIBRO NATO SULLE PAGINE DI QUALITIAMO
HAI DATO UN'OCCHIATA AL REGOLAMENTO DEL FORUM PRIMA DI SCRIVERE IL TUO MESSAGGIO? |
|
Top |
|
 |
|
 |
|
|
Non puoi inserire nuovi argomenti Non puoi rispondere a nessun argomento Non puoi modificare i tuoi messaggi Non puoi cancellare i tuoi messaggi Non puoi votare nei sondaggi
|
|