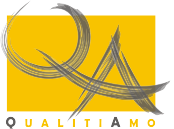 |
Il forum sulla Qualità di QualitiAmo Torna all'homepage di QualitiAmo
|
Precedente :: Successivo |
Autore |
Messaggio |
QualitiAmo - Stefania Moderatore

Registrato: 16/09/07 18:37 Messaggi: 26590
|
Inviato: Gio Lug 30, 2009 11:10 am Oggetto: La storia della Lean manufacturing |
|
|
Su SearchAutoParts potete leggere un articolo dal titolo: "The story of Lean".
Questa è la versione tradotta in italiano con il traduttore automatico di Google.
What is lean? Lean production is a manufacturing methodology originally developed by Toyota in the 1950s for the manufacturing of automobiles. Engineer Taiichi Ohno is credited with developing the Toyota Production System and, ultimately, lean production. He discovered that through enhancing quality, production automatically improved, and the waste of materials and resources was reduced, hence creating a lean enterprise. There were two other gentlemen who also helped shape the Toyota Production System. They were Shigeo Shingo, a quality consultant hired by Toyota, who assisted in the implementation of quality initiatives; and W. Edwards Deming, who brought Statistical Process Control to Japan. Today, there are many global automotive companies who have adopted “lean” principles in order to compete with Toyota and other Japanese automobile manufacturers.
The use of the term "lean" in a business or manufacturing environment describes a philosophy that incorporates a collection of tools and techniques into the business processes to optimize time, human resources, assets, and productivity, while improving the quality level of products and services to their customers. Lean production is all about managing and improving a workshop or business process so that you can deliver what the customer needs—profitably. In their landmark book The Machine That Changed the World, James Womack and Daniel Jones, two of the top industrial analysts in the world, explained how companies can dramatically improve their performance through the lean production approach pioneered by Toyota.
The phenomena of lean production principles are that they will work anywhere and in any type of business — they are universal. Lean principles have proven not only to be universal, but to be universally successful at improving results. One of the major building blocks of the Toyota Production System is the continuous improvement process (kaizen). It is through implementation and integration of continuous improvement processes that your collision repair business is able to benefit by reducing costs, improving quality, and increasing productivity. It is important for you to realize, upfront, that making your operational processes “lean” is a major learning experience and requires a total commitment from your management team and staff.
Ten rules of lean production in summary are as follows:
1. Eliminate all unnecessary waste
2. Minimize excess inventory
3. Maximize production flow
4. Prioritize production from customer order requests
5. Meet customer requirements
6. Always do it right the first time
7. Empower workers to find problems
8. Design for rapid changeover
9. Partner with suppliers
10. Create a system of continuous improvement
How can these lean production principles yield extraordinary benefits to the collision repair industry? Can we really improve our quality, raise the production flow, and drive down our operating costs as a result of implementing the lean principles? The reason for the broad industry acceptance of Lean Thinking is that the principles are well thought out, proven, and can lead to dramatic results.
The main principles are teamwork, communication, efficient use of resources and elimination of waste, and continuous improvement. All of these are key business drivers that can help any business become more efficient and effective at what they do, whether it is a service provider or a manufacturing company. The first step in applying this revolutionary approach to business processes is learning to identify waste. If you become extremely aware of waste, you will be able to recognize it and eliminate the root cause of it immediately.
The collision repair industry provides us with many opportunities to eliminate excess waste. A few of the most common are waste in inventory, waste in time and material, waste in extra steps/procedures, and waste in excessive facility capacity and equipment. In order to begin to eliminate waste, it will be necessary to empower your technicians to systematically trace every error or mistake back to its root cause and then to devise a solution so that it never occurs again. This does not imply that you should punish your staff for waste, but, conversely, you must challenge them to identify waste when they see it or experience it. You will need to enlist their help in driving out waste in all of its forms; therefore, it is absolutely essential to get their open and honest feedback, which requires a fear-free environment.
Consider this. What amount of time and money are spent when we are inspecting the vehicle’s repair quality at the end-of-the-line? How much does it cost to rectify problems and defects at this point? In many situations, the customer has taken on the role of the quality control inspector in order to ensure that their expectations have been met. This scenario creates a dissatisfied customer, and it always costs the collision repair shop more than the direct costs of correcting the quality related issues. Indirect costs stemming from this practice are enormous and often overlooked; e.g., lost opportunities, insurance company relationships, employee moral, and the company’s image in the market place. Quality has to be built into the product during the entire repair process—quality cannot be inspected into the finished product. If quality inspectors are evaluating vehicles that are completely done, it’s too late and too costly to make the right quality adjustments at that stage. To achieve the goal of “lean production,” you must eliminate all of the production process defects and errors, and then, and only then, will you have a higher quality product, which actually costs your organization less money to produce. The final result of “lean” is a higher quality product (adding nothing but value), produced faster, and at a lower cost than your competitor — this demonstrates the power of a lean production process.
After reading the book The Machine That Changed the World, I went to work on designing and developing a flow chart model to illustrate the lean production process as it applies to the collision repair environment. And, I recall how excited I was to share it with someone in the collision repair industry; although this was some five-years ago, it still seems like yesterday to me. So, I sought out a good friend of mine who owns a collision repair shop, and I was anticipating him to be ecstatic when I opened my briefcase and out popped my laminated “Lean Production” flow chart. He studied it for a few minutes with this morose look all over his face, and I began badgering him to tell me what he thought, expecting nothing but the highest praise and accolades.
He finally looked right into my eyes and said, “This will never work, and it just won’t work in a body shop environment.”
Well, several years have gone by since then; and, as things certainly do change, I will tell you, that same person has become a major proponent of “lean.” He has been at work for the last three-years building a lean culture and work environment at his shop, which has already proven to deliver the phenomenal results that we had discussed some five-years earlier. _________________ Stefania - Staff di QualitiAmo
ISO 9001:2015 - SI AGGIUNGE ALLA COLLANA DEI LIBRI DI QUALITIAMO IL NUOVO TESTO CHE SVELA I SEGRETI DELLA FUTURA NORMA
IL PRIMO LIBRO NATO SULLE PAGINE DI QUALITIAMO
HAI DATO UN'OCCHIATA AL REGOLAMENTO DEL FORUM PRIMA DI SCRIVERE IL TUO MESSAGGIO? |
|
Top |
|
 |
|
 |
|
|
Non puoi inserire nuovi argomenti Non puoi rispondere a nessun argomento Non puoi modificare i tuoi messaggi Non puoi cancellare i tuoi messaggi Non puoi votare nei sondaggi
|
|